DC motors are motion components that take electrical power in the form of direct current (or some manipulated form of direct current) and convert it into mechanical rotation. The motors do this through the use of magnetic fields that arise from the electric currents to spur rotation of a rotor fixed with an output shaft. Output torque and speed depends on the electrical input and motor design.
In this Design Guide, the editors of Design World detail the most common DC motor types as well common ways to quantify their output during the design engineering process.
Get your copy of the complete Brushless DC Motors Design Guide today!
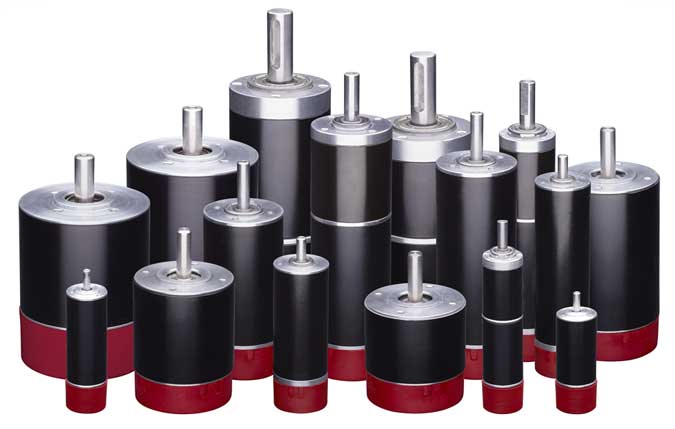
Table of Contents
- DC motor construction and operation
- Brushless DC motor specifics
- Considering DC motors’ hall sensors
- Deeper dive on linear behavior
- Difference between slotted and slotless motors
- Details on voltage and DC motor output speed
- The relationship between current and output torque
- Ways to avoid torque ripple in DC motors
Download the complete Brushless DC Motors Design Guide
Excerpt
Brushless DC (BLDC) motors do away with mechanical commutation in favor of electronic commutation, which avoids mechanical wear as exhibited by brushed DC motors. In most BLDC motors, permanent magnets are on the rotor and coils in the stator. The coil windings produce a rotating magnetic field because they’re electrically separated so can be independently turned on and off.
In a BLDC motor, contacting brush-and-copper commutation doesn’t bring current to the rotor. Instead, the rotor’s permanent magnet field trails the rotating stator field with its rotor field.
Brushless DC (BLDC) motors use magnets for commutation.
In this way, brushless DC motors work like shunt-wound motors, but field flux comes from magnets instead of current through a winding. The permanent magnets are made of rare-earth elements such as high-energy neodymium that generate magnetic fields.
Note some naming-convention caveats: Permanent-magnet (PM) DC motors with brushes (for mechanical commutation) are often called PMDC motors. But motors commonly called brushless DC motors have permanent magnets (PMs) so they are technically PM synchronous motors that run on ac (though through a DC bus and electronic inverter circuitry). That’s why some manufacturers avoid the use of BLDC and instead call these motors electronically commutated or EC motors.
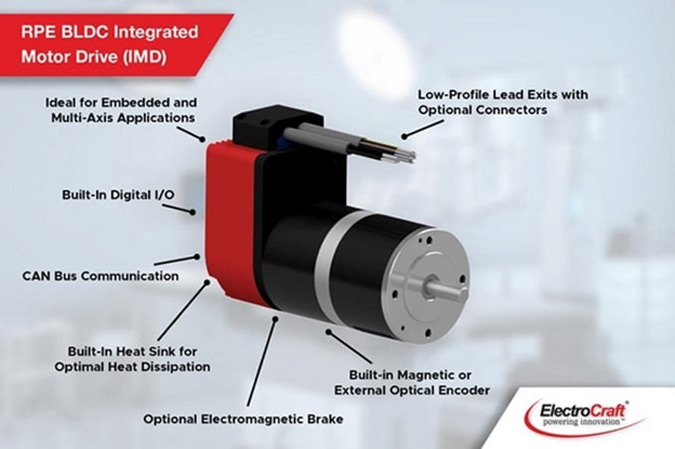
The BLDC naming convention merely indicates that:
- These motors don’t run directly from ac lines and
- These motors (with the proper drives) can replace DC brush motors (paired with drives) in closed-loop applications.
Most permanent-magnet DC motors drive fractional-horsepower applications though other uses are on the rise. Output torque is proportional to armature (rotor) current over the motor’s speed range.